Guide: A soap manufacturing and processing factory enterprise in Pakistan ordered a 8 ton biomass fired boiler use for there production.
This is the first time cooperation of this local enterprise specializing in soap manufacturing and processing in Pakistan with Xinli Boiler. The company learned about Xinli Boiler through online information, then chose Xinli Boiler as its boiler supplier after conducting multiple investigations and comparisons. Soap needs to go through processes such as refining, saponification, salt precipitation, and washing before it can be made. The saponification process requires the introduction of steam and stirring of the soap material among these processes, while the washing process requires the addition of water and steam to boil the soap particles for washing out residual glycerol, pigments, and impurities. Therefore, the enterprise ordered a DZL series biomass fired steam boiler with steam output of 8 tons from Xinli Boiler for the thermal energy supply of its production line based on the production status. Our business manager actively communicated project technology and solutions with the customer, timely got and followed up on their specific needs for boilers, and provided strong support to meet their professional production needs throughout the entire cooperation and communication process.
This kind of boiler has a wide range of fuel options, including combustible fuels such as bituminous coal, lean coal, anthracite, and biomass pellets. The user can choose suitable boiler fuels to support their production based on their actual needs. On the other hand, this series of boilers is assembled from the factory and consists of two parts: the upper part is the heating surface of the main body, and the lower part is the combustion equipment. It reduces the technical requirements for boiler installation, and the installation cycle of the boiler after arriving at the customer's project site is relatively short, which has the advantage of easy installation. In addition, the grate is equipped with different numbers of independent air silos from front to back depending on the tonnage of the boiler. The customer can allocate air reasonably according to different combustion conditions to ensure sufficient fuel combustion, and the boiler thermal efficiency can reach over 82%. After the boiler components are delivered to the customer's project site, they can be put into running by connecting pipes, valves, smoke and air ducts, and control circuits. At present, the boiler has been shipped from Xinli Boiler's factory.
More information on Facebook:
https://www.facebook.com/permalink.php?story_fbid=pfbid0gCwDAdFVMzpy5nDwMtsZhTErvQrJTZryfSqSRDFHayxBNTvdrzikKDAyzs367zQsl&id=100054631516411
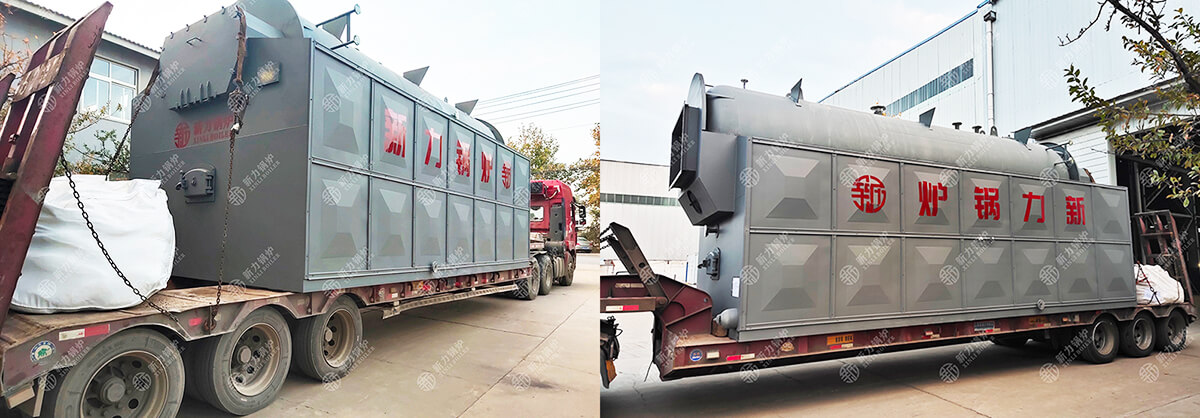