Guide: A textile factory supplier of ZARA and GAP in Pakistan ordered a 2.4 million kcal coal fired thermal oil boiler from Xinli Boiler for their production line.
Xinli Boiler has been exported overseas and has gained the trust of many enterprises in the Pakistan with its significant advantages in technology and quality. One of the Pakistan textile enterprises as a supplier with full industrial chain production capacity of globally renowned clothing brands such as ZARA and GAP has received popularity in the global market for its products. The high energy consumption processes such as washing, dyeing, printing, and post-processing required by textile enterprises need to be carried out at high temperatures, and thermal oil heaters are essential heat source equipment in the textile industry. With the booming development of its business, the company decided expand its business and they signed the contact with Xinli Boiler on the YLW series coal fired thermal oil boiler. In the base of the boiler, Xinli Boiler has improved and optimized the design of the grate and arch based on the characteristics of the coal used by the customer.The technical team of Xinli Boiler also set up multiple independent air silos and dampers to achieve uniform and full combustion of coal and improve fuel utilization. In the boiler body section, Xinli Boiler’s technical team uses high-quality insulation materials and special construction techniques to minimize heat loss as much as possible.
Xinli Boiler provided the customer with a YLW series coal fired thermal oil boiler with a capacity of 2.4 million kcal. This coal fired thermal oil boiler adopts a multi loop square coil design, coupled with efficient insulation materials and advanced construction technology, which can generate higher temperatures at lower pressures and achieve ideal thermal efficiency. The actual thermal efficiency of the boiler is over 85% after testing in factory. At the same time, the boiler is equipped with a fully automatic intelligent control system that can adjust the boiler parameters according to the specific operating environment of the user with a high degree of automation and stable safety performance. The boiler adopts an advanced structural form and optimized the radiation heating surface. It can reduce the formation and emission of smoke and dust in the combustion chamber. In addition, the setting of an effective ash removal structure facilitates the maintenance, operation, and cleaning of the boiler.
More information on Facebook:
https://www.facebook.com/permalink.php?story_fbid=pfbid0eLJEFE6DVFQrHt6Z1CUNWdnhNoYaHUNcxN76nJaBMQaguhcZv4K6KmgJxBPVgrVql&id=100054631516411
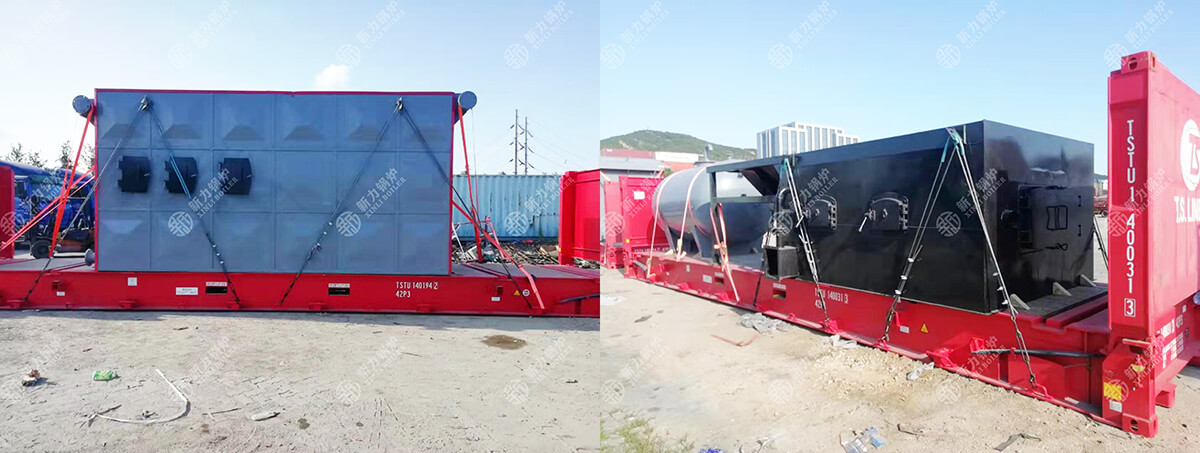