Guide: A waste paper recycling manufacturing enterprise purchased a 20 ton of coal and biomass fired steam boiler used for their paper production.
A waste paper recycling manufacturing enterprise established in 2010 in Indonesia plans to invest in and construct an additional 50000 tons of grey cardboard expansion project to meet market demand. The project will introduce new papermaking equipment and a coal biomass boiler, while phasing out outdated production equipment and upgrading existing pollution control facilities. The SZL series coal biomass fired steam boiler under Xinli Boiler has successfully gained the favor of the customer due to its excellent efficiency and environmental performance, providing a stable and reliable steam heat source for the dehydration molding, drying and other processes in the production of grey cardboard. Steam is mainly used for heating and drying pulp, effectively removing moisture from the paper manufacturing process, which is the key to ensuring paper quality and production efficiency. High quality steam also means better heat transfer efficiency, which directly improves the energy utilization rate of the production process. The coal biomass fired steam boiler produced by Xinli Boiler has a unique design structure and production process, which first solves common problems that occur in traditional biomass boilers, such as furnace arch collapse, furnace door burnout, hopper ignition, and stopper coking. At the same time, its safety, efficiency, energy-saving and environmental protection characteristics are also very significant, and it has established a good reputation in the market.
Xinli Boiler's sales manager recommended a 20 ton SZL series coal and biomass dual fuels fired steam boiler solution after knowing the demand of the customer. This coal and biomass fired boiler not only has the above advantages, but also is an assembled boiler with compact structure, easy on-site installation, short cycle and low cost, meeting the urgent needs of the company's production line. Xinli Boiler's technical team also conducts rational design optimization on the feeding hopper, grate width, length, etc based on the characteristics of the fuel. The large furnace volume reduces the heat load and minimizes the occurrence of coking inside the furnace. In addition, the boiler grate adopts a lightweight chain belt grate, and segmented air chambers and air regulating devices are arranged under the grate to meet the required air volume of the fuel at different combustion stages, achieve precise air distribution, ensure full combustion of the fuel, and achieve a thermal efficiency of over 88%. All indicators have reached the international advanced level. Xinli Boiler successfully completed the production and manufacturing of the boiler within the agreed delivery date. The picture shows the delivery site of the boiler.
More information on Facebook:
https://www.facebook.com/Xinli.Boiler.Co/posts/pfbid0qKaBjaiWJ8S5MDUhDnJDFTLZ1PczTdjkbXj1afV6d6Deo6gMtDHKwwXkpgSWLNFJl
More information on LinkedIn:
https://www.linkedin.com/posts/boiler-xinli-917522197_steamboiler-coalboiler-biomassboiler-activity-7262360621726203906-ZZX4?utm_source=share&utm_medium=member_desktop
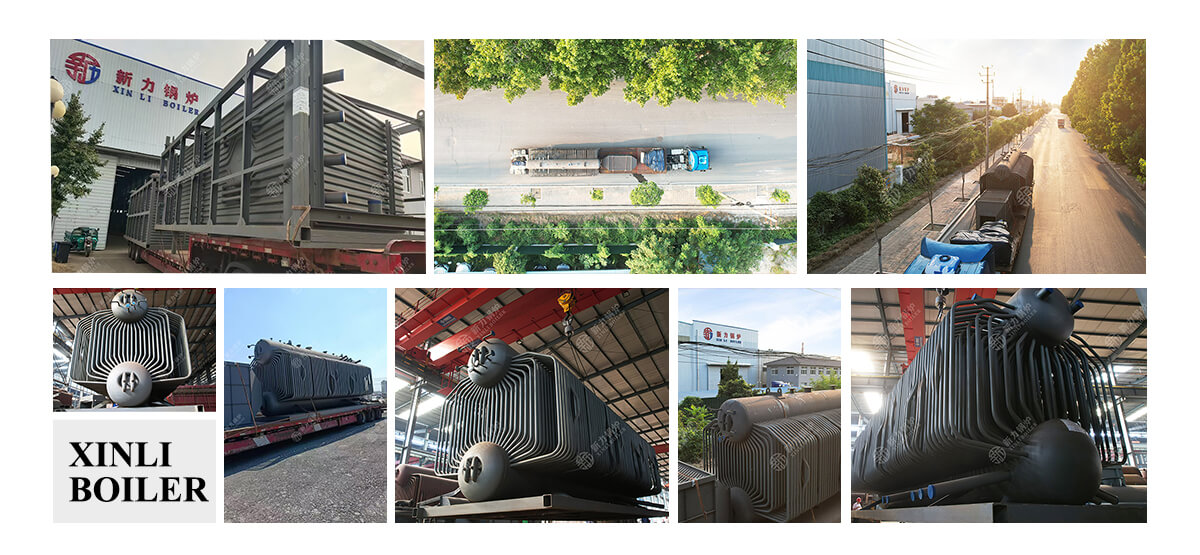